中國冶金報 中國鋼鐵新聞網(wǎng)
王國棟 儲滿(mǎn)生 袁國 秦高梧 韓躍新 張殿華 張琦
鋼鐵產(chǎn)業(yè)碳中和背景及其實(shí)現路徑
鋼鐵產(chǎn)業(yè)是國民經(jīng)濟發(fā)展的支柱產(chǎn)業(yè)。我國是世界第一鋼鐵大國,2020年粗鋼產(chǎn)量達到10.65億噸,占全球粗鋼總產(chǎn)量的56%,但我國鋼鐵生產(chǎn)以高爐-轉爐長(cháng)流程為主,嚴重依賴(lài)煤基化石能源,是導致碳排放量較高的首要因素。2020年,鋼鐵產(chǎn)業(yè)二氧化碳排放量占我國碳排放總量的16%左右。有效降低二氧化碳排放強度和加強碳捕捉利用是鋼鐵產(chǎn)業(yè)亟待解決的難題,也是國家的重大戰略需求。因此,鋼鐵產(chǎn)業(yè)亟待研發(fā)和應用碳中和前沿技術(shù),實(shí)現低碳綠色化轉型升級。即將實(shí)施的碳稅政策更凸顯其倒逼作用,將對資源能源密集型的鋼鐵產(chǎn)業(yè)產(chǎn)生直接深遠的影響。
從技術(shù)層面來(lái)看,鋼鐵產(chǎn)業(yè)實(shí)現碳中和主要包括以下幾步:
第一步,針對碳達峰和碳減排平臺階段,研發(fā)和應用低碳冶煉與全流程低碳加工及智能制造技術(shù),實(shí)現高能效和低碳化。在工藝優(yōu)化、強化冶煉、余熱和二次資源高效循環(huán)利用、超低排放改造、系統節能、產(chǎn)品高質(zhì)化等基礎上,研發(fā)應用低碳高爐、高效連鑄、鑄軋一體化、在線(xiàn)組織性能調控等低碳冶煉、加工新技術(shù),同時(shí)開(kāi)發(fā)全流程信息物理系統,實(shí)現高可靠性、高穩定性全流程智能制造,最大程度地提高能源利用效率和實(shí)現碳減排,為碳中和奠定基礎。
第二步,針對鋼鐵產(chǎn)業(yè)快速降碳階段,在低碳高能效冶煉基礎上,研發(fā)和應用鋼鐵-化工聯(lián)產(chǎn)技術(shù)(見(jiàn)圖1),增加碳匯,實(shí)現碳凈零排放?;谔疾都?,研發(fā)應用鋼鐵-化工-氫能一體化網(wǎng)絡(luò )集成CCU技術(shù)(steel-chemicals-energy networking integration,簡(jiǎn)寫(xiě)為SCENWI,也稱(chēng)神威CCU技術(shù)),通過(guò)鋼鐵-化工協(xié)同,為我國以高爐-轉爐長(cháng)流程為主的鋼鐵產(chǎn)業(yè)實(shí)現碳凈零排放提供最合理、最徹底的解決方案。
第三步,針對鋼鐵產(chǎn)業(yè)深度脫碳階段,在低碳高能效和鋼鐵-化工聯(lián)產(chǎn)基礎上,輔以氫能替代化石能源,研發(fā)應用氫基豎爐-電爐短流程新工藝技術(shù),在適宜區域實(shí)現鋼鐵工藝流程革新和能源結構優(yōu)化,為深脫碳或無(wú)涉碳鋼鐵生產(chǎn)提供全新途徑。
與國外相比,國內目前在氫冶金、鋼鐵-化工聯(lián)產(chǎn)等碳中和前沿技術(shù)研發(fā)方面尚處于起步階段,工業(yè)化應用較多處于空白,總體屬于“跟跑”階段。因此,碳中和冶煉極有可能成為制約我國鋼鐵工業(yè)未來(lái)發(fā)展的“卡脖子”技術(shù)。由于國外技術(shù)保密和限制,我國今后在核心技術(shù)應用方面極易受制于人,急需加快碳中和冶金研發(fā)步伐,突破關(guān)鍵技術(shù),打破國外技術(shù)封鎖,搶占低碳前沿陣地,實(shí)現核心技術(shù)、關(guān)鍵裝備、標準體系、研發(fā)平臺和人才隊伍的全面超越,引領(lǐng)鋼鐵產(chǎn)業(yè)低碳綠色化發(fā)展。
鋼鐵產(chǎn)業(yè)是國民經(jīng)濟發(fā)展的支柱產(chǎn)業(yè)。我國是世界第一鋼鐵大國,2020年粗鋼產(chǎn)量達到10.65億噸,占全球粗鋼總產(chǎn)量的56%,但我國鋼鐵生產(chǎn)以高爐-轉爐長(cháng)流程為主,嚴重依賴(lài)煤基化石能源,是導致碳排放量較高的首要因素。2020年,鋼鐵產(chǎn)業(yè)二氧化碳排放量占我國碳排放總量的16%左右。有效降低二氧化碳排放強度和加強碳捕捉利用是鋼鐵產(chǎn)業(yè)亟待解決的難題,也是國家的重大戰略需求。因此,鋼鐵產(chǎn)業(yè)亟待研發(fā)和應用碳中和前沿技術(shù),實(shí)現低碳綠色化轉型升級。即將實(shí)施的碳稅政策更凸顯其倒逼作用,將對資源能源密集型的鋼鐵產(chǎn)業(yè)產(chǎn)生直接深遠的影響。
從技術(shù)層面來(lái)看,鋼鐵產(chǎn)業(yè)實(shí)現碳中和主要包括以下幾步:
第一步,針對碳達峰和碳減排平臺階段,研發(fā)和應用低碳冶煉與全流程低碳加工及智能制造技術(shù),實(shí)現高能效和低碳化。在工藝優(yōu)化、強化冶煉、余熱和二次資源高效循環(huán)利用、超低排放改造、系統節能、產(chǎn)品高質(zhì)化等基礎上,研發(fā)應用低碳高爐、高效連鑄、鑄軋一體化、在線(xiàn)組織性能調控等低碳冶煉、加工新技術(shù),同時(shí)開(kāi)發(fā)全流程信息物理系統,實(shí)現高可靠性、高穩定性全流程智能制造,最大程度地提高能源利用效率和實(shí)現碳減排,為碳中和奠定基礎。
第二步,針對鋼鐵產(chǎn)業(yè)快速降碳階段,在低碳高能效冶煉基礎上,研發(fā)和應用鋼鐵-化工聯(lián)產(chǎn)技術(shù)(見(jiàn)圖1),增加碳匯,實(shí)現碳凈零排放?;谔疾都?,研發(fā)應用鋼鐵-化工-氫能一體化網(wǎng)絡(luò )集成CCU技術(shù)(steel-chemicals-energy networking integration,簡(jiǎn)寫(xiě)為SCENWI,也稱(chēng)神威CCU技術(shù)),通過(guò)鋼鐵-化工協(xié)同,為我國以高爐-轉爐長(cháng)流程為主的鋼鐵產(chǎn)業(yè)實(shí)現碳凈零排放提供最合理、最徹底的解決方案。
第三步,針對鋼鐵產(chǎn)業(yè)深度脫碳階段,在低碳高能效和鋼鐵-化工聯(lián)產(chǎn)基礎上,輔以氫能替代化石能源,研發(fā)應用氫基豎爐-電爐短流程新工藝技術(shù),在適宜區域實(shí)現鋼鐵工藝流程革新和能源結構優(yōu)化,為深脫碳或無(wú)涉碳鋼鐵生產(chǎn)提供全新途徑。
與國外相比,國內目前在氫冶金、鋼鐵-化工聯(lián)產(chǎn)等碳中和前沿技術(shù)研發(fā)方面尚處于起步階段,工業(yè)化應用較多處于空白,總體屬于“跟跑”階段。因此,碳中和冶煉極有可能成為制約我國鋼鐵工業(yè)未來(lái)發(fā)展的“卡脖子”技術(shù)。由于國外技術(shù)保密和限制,我國今后在核心技術(shù)應用方面極易受制于人,急需加快碳中和冶金研發(fā)步伐,突破關(guān)鍵技術(shù),打破國外技術(shù)封鎖,搶占低碳前沿陣地,實(shí)現核心技術(shù)、關(guān)鍵裝備、標準體系、研發(fā)平臺和人才隊伍的全面超越,引領(lǐng)鋼鐵產(chǎn)業(yè)低碳綠色化發(fā)展。
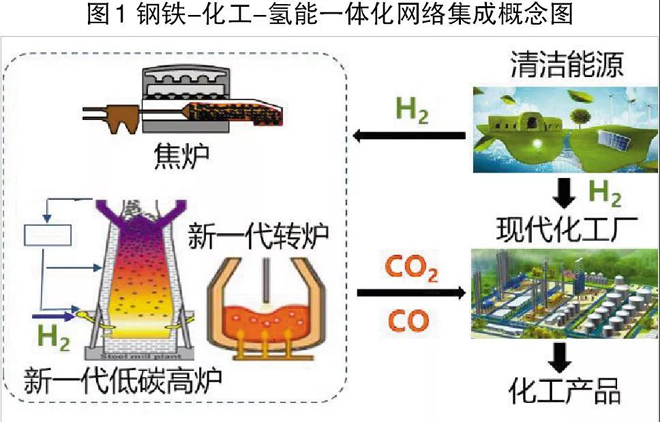
東大的鋼鐵碳中和技術(shù)路線(xiàn)
在上述背景下,東北大學(xué)成立低碳鋼鐵前沿技術(shù)研究院,協(xié)同研發(fā)氫冶金、鋼鐵-化工聯(lián)產(chǎn)、跨工業(yè)系統智能制造等低碳關(guān)鍵共性前沿技術(shù)(見(jiàn)圖2),提出了CCU技術(shù)。
神威CCU技術(shù)首先解決氫能來(lái)源問(wèn)題,在鋼廠(chǎng)內部副產(chǎn)煤氣制氫、化石能源制氫和石化廢氫(灰氫和藍氫)基礎上,重點(diǎn)開(kāi)發(fā)可再生能源發(fā)電、高效電解水制氫(綠氫),進(jìn)而研發(fā)富氫還原高爐煉鐵、氫基豎爐直接還原-電爐短流程技術(shù),實(shí)現氫冶金低碳冶煉。同時(shí),基于二氧化碳捕集利用思想,將鋼鐵生產(chǎn)的尾氣進(jìn)行高效低成本凈化、捕集、分離,得到一氧化碳和二氧化碳,作為化工產(chǎn)業(yè)的原料氣,用于合成甲酸、乙酸、乙醇及其他化工產(chǎn)品,通過(guò)鋼鐵-化工產(chǎn)業(yè)協(xié)同實(shí)現鋼鐵產(chǎn)業(yè)二氧化碳凈零排放。
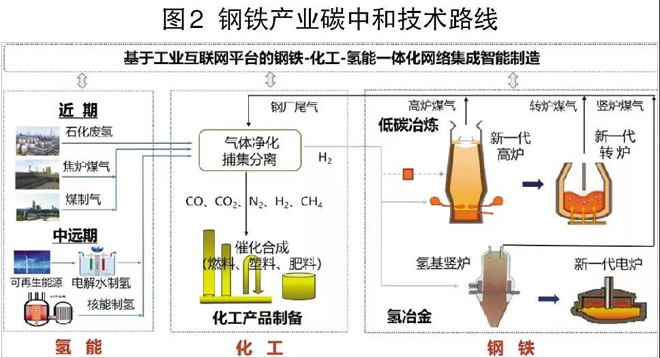
東大的鋼鐵碳中和關(guān)鍵技術(shù)研究
低碳冶煉技術(shù)
在國家“2011”計劃(高等學(xué)校創(chuàng )新能力提升計劃)支持下,東北大學(xué)礦冶學(xué)科群以“工藝綠色化、裝備智能化、產(chǎn)品高質(zhì)化”為目標,開(kāi)展了鋼鐵全流程一體化協(xié)同創(chuàng )新,研發(fā)了一系列低碳綠色化關(guān)鍵共性技術(shù),主要包括以下內容:
1.選礦
難選鐵礦石懸浮磁化焙燒技術(shù)。東北大學(xué)自主研發(fā)了“預氧化-蓄熱還原-再氧化”懸浮磁化焙燒新技術(shù),成功開(kāi)發(fā)懸浮焙燒工業(yè)化裝備與高效分選系統,填補國內外技術(shù)空白,實(shí)現貧雜赤鐵礦、菱鐵礦、褐鐵礦石及含鐵固廢等資源高效利用,盤(pán)活國產(chǎn)鐵礦資源100億噸以上,提高難選鐵礦石回收率15個(gè)百分點(diǎn)以上,提高鐵精礦品位3個(gè)百分點(diǎn)~10個(gè)百分點(diǎn),大幅降低采礦、冶煉工序碳排放量。
新型常溫高效鐵礦石浮選藥劑。傳統浮選藥劑凝固點(diǎn)高,分散性差,礦漿需加溫40攝氏度以上,能源浪費和環(huán)境污染嚴重,開(kāi)發(fā)貧雜鐵礦石常溫高效浮選藥劑體系迫在眉睫。為此,東北大學(xué)自主研發(fā)新型常溫高效鐵礦石浮選藥劑體系,根據藥劑極性基團活性原子的電子態(tài)密度與礦物表面活性位點(diǎn)原子的電子態(tài)密度匹配關(guān)系,開(kāi)發(fā)TD-Ⅱ、HBGT-135等新型浮選藥劑,解決浮選過(guò)程能耗高、效率差等問(wèn)題。
新型陶瓷介質(zhì)攪拌磨機技術(shù)。在選礦各環(huán)節中,磨礦成本占總成本的50%以上。開(kāi)發(fā)新型高效綠色磨礦技術(shù),努力降低球耗與電耗,成為礦山降本增效的重要課題。東北大學(xué)自主研發(fā)新型陶瓷介質(zhì)攪拌磨機在鞍鋼弓長(cháng)嶺選礦廠(chǎng)工業(yè)應用,球耗成本降低55.61%以上,磨礦電耗降低50.26%,磨礦單體解離度提高11.31%,選別指標提高0.2個(gè)百分點(diǎn),預計年綜合經(jīng)濟效益達到1600多萬(wàn)元。
2.煉鐵
低碳高爐集成技術(shù)。東北大學(xué)與多家鋼企合作研發(fā)富氫煤氣噴吹、復合鐵焦、爐頂煤氣循環(huán)-高富氧冶煉優(yōu)化匹配的低碳高爐煉鐵技術(shù),研究結果表明噴吹焦爐煤氣137立方米/噸鐵,頂煤氣循環(huán)率為48.8%,鼓風(fēng)富氧率為71.7%,則高爐噸鐵能耗降低22.1%、碳排放降低51.8%。目前正在進(jìn)行關(guān)鍵技術(shù)的工業(yè)化試驗。
3.煉鋼、精煉和連鑄
轉爐高廢鋼比冶煉技術(shù)。東北大學(xué)重點(diǎn)研發(fā)氧燃法廢鋼預熱、復吹轉爐高效冶煉技術(shù)與裝備,主要特點(diǎn)有:采用模塊化設計,根據企業(yè)裝備及空間而定制設計;集成多工況燃控模型、高效氧燃槍與燃控自動(dòng)化技術(shù);快速升溫,10分鐘加熱到800攝氏度以上;成本低,低熱值煤氣消耗200立方米/噸廢鋼~300立方米/噸廢鋼;噸鋼鐵水比降低30千克,二氧化碳減排50千克。
高效連鑄關(guān)鍵技術(shù)。東北大學(xué)自主研發(fā)形成以連鑄坯凝固末端重壓下、微合金鋼表面裂紋控制為代表的高效連鑄關(guān)鍵技術(shù),開(kāi)辟表面無(wú)缺陷、低軋制壓縮比高效生產(chǎn)高端鋼材新流程。與常規模鑄制坯相比,金屬收得率提升近15%,噸鋼節約標煤1.32千克;實(shí)現微合金鋼熱裝送,噸鋼節約標煤20千克~30千克。該技術(shù)已在中國寶武等國內外鋼企的29條產(chǎn)線(xiàn)推廣應用,獲得國家科技進(jìn)步獎1項、省部級一等獎5項。
電弧爐高效冶煉技術(shù)。東北大學(xué)自主開(kāi)發(fā)形成電弧爐節能煉鋼、快速熔煉等全套電弧爐高效冶煉技術(shù),實(shí)現全廢鋼電弧爐短流程低成本環(huán)境友好高效冶煉技術(shù)的國產(chǎn)化;能耗降低20%以上,噸鋼碳排放降至667千克,冶煉周期縮短約40%,效率提高50%以上,運行成本降低30%以上。該技術(shù)已在中國寶武等鋼企的多座電弧爐上推廣應用,并在江蘇金虹公司投產(chǎn)國內首條低成本環(huán)境友好型全廢鋼電弧爐高效熔煉短流程生產(chǎn)線(xiàn),達到國際領(lǐng)先水平。
高品質(zhì)特殊鋼電渣重熔關(guān)鍵技術(shù)。東北大學(xué)自主研發(fā)形成以全參數過(guò)程穩定的電渣重熔潔凈度控制為代表的高品質(zhì)特殊鋼電渣重熔關(guān)鍵技術(shù),解決了國家重大工程和重大裝備用多種“卡脖子”材料急需。與傳統工藝相比,該技術(shù)能耗和碳排放降低效果顯著(zhù),已推廣應用于60多家特鋼企業(yè),獲得國家科技進(jìn)步獎一等獎1項、省部級一等獎3項。
4.軋鋼
新一代TMCP(控制軋制和控制冷卻技術(shù))理論技術(shù)與裝備研發(fā)及工程化。東北大學(xué)研發(fā)成功系列首臺(套)板、帶、管、型、棒、線(xiàn)材一體化在線(xiàn)組織調控核心裝備,成為我國熱軋鋼材生產(chǎn)線(xiàn)主力機型,覆蓋全部熱軋鋼材門(mén)類(lèi),推動(dòng)離線(xiàn)熱處理工藝在線(xiàn)化,節能降耗,提高產(chǎn)品品質(zhì)。該技術(shù)應用至寶鋼、鞍鋼、首鋼、河鋼等90%以上大型鋼企50余條生產(chǎn)線(xiàn),在鞍鋼、南鋼建成國家級示范線(xiàn),年創(chuàng )效益超百億元。
薄帶連鑄硅鋼基礎理論與產(chǎn)業(yè)化技術(shù)。通過(guò)基礎研究、工業(yè)化技術(shù)開(kāi)發(fā),東北大學(xué)研發(fā)了獨創(chuàng )的顛覆性工業(yè)技術(shù)和超高性能產(chǎn)品,開(kāi)發(fā)高磁感電工鋼薄帶鑄軋短流程工藝,目前已與敬業(yè)集團開(kāi)展產(chǎn)學(xué)研合作,開(kāi)展高品鋼薄帶鑄軋產(chǎn)業(yè)化項目,旨在開(kāi)發(fā)生產(chǎn)領(lǐng)先的高磁感硅鋼產(chǎn)品。
5.系統節能
智慧化能源管控系統。東北大學(xué)開(kāi)發(fā)能源管控系統,實(shí)現鋼企能源精益化管理,為節能和碳減排提供工具,其中智能化能源管控平臺項目在鞍鋼鲅魚(yú)圈分公司上線(xiàn)運行;煤氣預測與多介質(zhì)耦合優(yōu)化項目在首鋼京唐能源管控中心上線(xiàn)運行;與寶信合作承擔重點(diǎn)研發(fā)項目,在寶鋼股份上線(xiàn)運行。
全流程智能制造
鋼鐵工業(yè)屬于大型復雜流程工業(yè),涵蓋煉鐵-煉鋼-軋制-熱處理等工序,是充分發(fā)揮場(chǎng)景優(yōu)勢與數據資源優(yōu)勢的最佳載體,也是人工智能、大數據賦能產(chǎn)業(yè)增效的最具代表性領(lǐng)域,引領(lǐng)示范作用強。
東北大學(xué)提出依托云計算、大數據、5G+邊緣計算等先進(jìn)信息通信技術(shù),以信息物理系統為核心、工業(yè)互聯(lián)網(wǎng)為載體的鋼鐵全流程智能制造架構,取得了重要突破,形成自主知識產(chǎn)權和高質(zhì)量、低成本、高效率改造路徑與模式,已在鞍鋼、河鋼、華菱漣鋼、建龍集團撫順新鋼鐵實(shí)施中。
氫冶金
在我國能源轉型過(guò)程中,氫能扮演著(zhù)“高效低碳的二次能源、靈活智慧的能源載體、綠色清潔的工業(yè)原料”角色。綠色氫能被認為是無(wú)碳經(jīng)濟的關(guān)鍵之鑰,將氫能應用于冶金是冶金行業(yè)低碳綠色化轉型的有效途徑。一般意義上的氫冶金是指入爐還原氣含氫高于55%條件下,還原鐵礦石、球團礦生產(chǎn)優(yōu)質(zhì)DRI(直接還原鐵)的氣基豎爐直接還原?;跉湟苯鸬臍饣Q爐-電爐短流程具有碳減排50%以上潛力,是歐洲國家和美日等先進(jìn)產(chǎn)鋼國研發(fā)的熱點(diǎn)。
為基于我國原燃料條件發(fā)展氫冶金,東北大學(xué)進(jìn)行了以下研究工作:
高品位鐵精礦制備技術(shù)。基于河北、山西、吉林、遼寧、山東、湖北、安徽多地磁鐵礦資源(大于30億噸),成功開(kāi)發(fā)高品位鐵精礦(全鐵>70.5%、二氧化硅2.0%)制備技術(shù)和設備,建成年產(chǎn)10萬(wàn)噸高品位鐵精礦示范線(xiàn)。
氣基豎爐專(zhuān)用氧化球團制備技術(shù)。通過(guò)多地高品位鐵精礦的氧化焙燒試驗系統研究,結果基于國內鐵礦條件可生產(chǎn)冶金性能優(yōu)良的氣基豎爐專(zhuān)用氧化球團。
煤制氣-富氫豎爐示范工程設計。籌建富氫豎爐-電爐短流程示范工程,已完成整個(gè)工藝系統和工程設計,自主開(kāi)發(fā)了氣基豎爐核心裝置,形成了多項知識產(chǎn)權成果。
全氫氣基豎爐關(guān)鍵技術(shù)。與某大型鋼企合作,研發(fā)基于可再生能源制氫-全氫豎爐直接還原關(guān)鍵技術(shù),包括全氫豎爐爐料、工藝系統設計、重大工藝裝備、操作優(yōu)化、安全控制技術(shù)、智能冶煉。
鋼鐵-化工聯(lián)產(chǎn)
我國將來(lái)很長(cháng)一段時(shí)間鋼鐵生產(chǎn)仍將以高爐-轉爐流程為主,應在加強氫冶金研發(fā)的同時(shí),重點(diǎn)發(fā)展鋼鐵-化工聯(lián)產(chǎn)技術(shù),即將鋼鐵副產(chǎn)含一氧化碳、二氧化碳尾氣進(jìn)行捕集和分離,作為合成氣提供給化工廠(chǎng)用作加氫催化合成燃料、塑料、肥料等化工產(chǎn)品。這樣做既減少鋼鐵生產(chǎn)的二氧化碳排放,同時(shí)為化工行業(yè)輸入原本需要消耗化石或生物質(zhì)才能獲得的碳資源。另外,由于鋼鐵系統副產(chǎn)氫能不足,須引入新能源行業(yè),利用可再生能源制氫。因此,鋼鐵-化工聯(lián)產(chǎn)是通過(guò)鋼鐵、化工、氫能三大行業(yè)跨工業(yè)生產(chǎn)系統的網(wǎng)絡(luò )協(xié)作和一體化網(wǎng)絡(luò )集成,在保留高爐前提下實(shí)現高爐-轉爐長(cháng)流程最合理、最可持續的減排方式,也是通過(guò)鋼鐵-化工協(xié)同,實(shí)現碳排放趨零的最徹底的解決方案。
鋼鐵-化工聯(lián)產(chǎn)的難點(diǎn)主要體現在尾氣多級協(xié)同凈化捕集分離、二氧化碳高效催化合成、大規模低成本制氫、高附加值化工產(chǎn)品制備等方面。為此,東北大學(xué)開(kāi)展了以下研究工作:
尾氣高效凈化捕集技術(shù)及裝置。開(kāi)發(fā)國際領(lǐng)先的一步法高爐尾氣脫硫工藝,脫硫率達99.9%,比主流技術(shù)節省20%成本,并與相關(guān)企業(yè)合作研發(fā)了世界首套多塔重回流變壓吸附裝置。
尾氣高效吸附劑。開(kāi)發(fā)具有自主知識產(chǎn)權的離子液沸石、“分子陷阱門(mén)”材料等吸附劑,用于高效、低成本、選擇性吸附,在鋼廠(chǎng)尾氣、煙道氣、天然氣分離等領(lǐng)域具有廣泛應用前景。
二氧化碳液相催化還原制甲醇。研發(fā)銅納米顆粒催化劑和ZnZr離子交換的HTC催化劑,進(jìn)行了二氧化碳催化還原制甲醇的系統研究和工藝技術(shù)開(kāi)發(fā)。
二氧化碳加氫合成甲烷。結合載體界面電子效應和多組元設計,開(kāi)發(fā)高活性、高選擇性稀土氧化物負載的Ni催化劑,在常壓和300攝氏度條件下獲得轉化率99%以上的選擇性。
光催化二氧化碳還原制甲醇。以太陽(yáng)光為能源,以水或氫氣為還原劑,利用Ta3N5(五氮化三鉭)、Cu2O(氧化亞銅)基高效光催化劑,常溫常壓將二氧化碳轉化為甲醇,甲醇產(chǎn)率223.2μmol/g cat.,具有綠色、環(huán)保、節能優(yōu)點(diǎn)。
二氧化碳電催化制乙烯。以綠色電能為能源,通過(guò)電催化技術(shù)將鋼鐵尾氣中的二氧化碳轉變?yōu)橐蚁┑雀吒郊又祷瘜W(xué)品。隨著(zhù)太陽(yáng)能、風(fēng)能等清潔能源轉換為電能的成本不斷降低,電化學(xué)二氧化碳還原有望在可預期的將來(lái)規模部署。重點(diǎn)研究了催化中心結構精準構筑和高活性、高選擇性、長(cháng)壽命氣體擴散電極的制備。
合作研發(fā)二氧化碳微生物發(fā)酵法生產(chǎn)乙酸技術(shù)。合作單位以復合產(chǎn)乙酸菌將二氧化碳在常溫常壓條件下,加氫穩定高效轉化乙酸高附加值產(chǎn)品,攻克生物發(fā)酵法氣體溶解度低、產(chǎn)率低、選擇性差等難題,實(shí)驗室條件下實(shí)現二氧化碳和氫氣利用率達98%,產(chǎn)酸菌穩定性和選擇性遠高于現有其他技術(shù)。
鋼鐵-化工聯(lián)產(chǎn)技術(shù)中試。目前,東北大學(xué)與某鋼企合作建設鋼鐵碳中和關(guān)鍵技術(shù)中試基地,以高爐煤氣為氣源,進(jìn)行煤氣凈化和選擇性捕集分離、二氧化碳熱催化合成甲醇、電催化制乙烯、生物催化制乙酸的中試研究,以期擇優(yōu)選定技術(shù)經(jīng)濟性合理的二氧化碳轉化利用工藝路線(xiàn)。
在我國全面實(shí)現工業(yè)化進(jìn)程中,鋼鐵產(chǎn)業(yè)仍是起重要支撐和推動(dòng)作用的支柱產(chǎn)業(yè)。針對國家“30·60”碳減排目標,當前鋼鐵產(chǎn)業(yè)正處于低碳綠色化和數字智能化轉型關(guān)鍵時(shí)期。為此,鋼鐵產(chǎn)業(yè)應以節能高能效為基礎,重點(diǎn)發(fā)展多產(chǎn)業(yè)協(xié)同的碳捕捉利用,并輔以能源替代發(fā)展氫冶金,最終實(shí)現碳中和。
毋庸置疑的是,體量巨大的鋼鐵產(chǎn)業(yè)實(shí)現碳中和是一個(gè)相當艱巨的任務(wù),需要集聚全社會(huì )的優(yōu)勢力量,通過(guò)產(chǎn)學(xué)研用深度融合、多行業(yè)協(xié)同和多學(xué)科交叉,構建以“基礎-研發(fā)-工程-應用”為框架的鋼鐵行業(yè)科技創(chuàng )新完整全鏈條,以點(diǎn)帶面實(shí)現關(guān)鍵共性技術(shù)重大突破,最終形成在鋼鐵-化工-新能源-建材-高端裝備制造等組成的新產(chǎn)業(yè)鏈中起到重要中樞節點(diǎn)功能的全新鋼鐵產(chǎn)業(yè)。