編者按
能效提升是鋼鐵工業(yè)實(shí)現綠色低碳高質(zhì)量發(fā)展的核心舉措?!半p碳”目標提出以來(lái),我國鋼鐵產(chǎn)業(yè)結構持續優(yōu)化,節能工作取得積極成效。中國鋼鐵工業(yè)協(xié)會(huì )數據顯示,重點(diǎn)統計鋼鐵企業(yè)噸鋼綜合能耗由2012年的602.7千克標準煤/噸下降至2022年的551.4千克標準煤/噸。國家相關(guān)部委以及《“十四五”現代能源體系規劃》等政策文件對能源轉型提出了新要求;2022年12月9日,《鋼鐵行業(yè)能效標桿三年行動(dòng)方案》正式啟動(dòng),第三大鋼鐵改造工程——極致能效工程進(jìn)入實(shí)質(zhì)性實(shí)施階段。結合國家要求及行業(yè)形勢,鋼鐵企業(yè)應當堅定不移地發(fā)揮自身的能源轉換功能優(yōu)勢及能效潛力,創(chuàng )新優(yōu)化能源結構,突出原料用能導向,實(shí)現綠色低碳高質(zhì)量發(fā)展。本文結合實(shí)際談?wù)剬︿撹F行業(yè)推進(jìn)極致能效工程的思考和建議,上篇主題為“挖掘能源轉換潛力,實(shí)現極致能效提升”,下篇主題為“創(chuàng )新優(yōu)化能源結構,助力鋼鐵流程碳中和”。本期為上篇。
我國鋼鐵工業(yè)以高爐—轉爐長(cháng)流程生產(chǎn)為主,一次能源消耗結構主要為煤炭,節能降碳、改造升級潛力較大。國家在能效方面啟動(dòng)的相關(guān)工作,意在以能效標桿為切入點(diǎn),全面提升鋼鐵行業(yè)的競爭力,實(shí)現綠色低碳高質(zhì)量發(fā)展。
能效提升是目前鋼鐵行業(yè)減碳的優(yōu)先工作,是一項系統工程。筆者認為,鋼鐵企業(yè)應深度開(kāi)發(fā)能源轉換功能價(jià)值,以實(shí)現極致能效提升,主要路徑包括主體工序能耗達標、余熱深度回收及梯級利用、能源網(wǎng)絡(luò )分布式耦合優(yōu)化、煤氣發(fā)電能效(自發(fā)電)提升、跨行業(yè)協(xié)同與碳氫元素原料利用耦合等。
主體工序達能效標桿值比例較低
著(zhù)力推動(dòng)到2025年超30%產(chǎn)能達標
國家發(fā)展改革委發(fā)布的《關(guān)于嚴格能效約束推動(dòng)重點(diǎn)領(lǐng)域節能降碳的若干意見(jiàn)》提出:到2025年,通過(guò)實(shí)施節能降碳行動(dòng),鋼鐵等重點(diǎn)行業(yè)達到標桿水平的產(chǎn)能比例超過(guò)30%,行業(yè)整體能效水平明顯提升,碳排放強度明顯下降,綠色低碳發(fā)展能力顯著(zhù)增強。到2030年,重點(diǎn)行業(yè)能效基準水平和標桿水平進(jìn)一步提高,達到標桿水平企業(yè)比例大幅提升,行業(yè)整體能效水平和碳排放強度達到國際先進(jìn)水平。
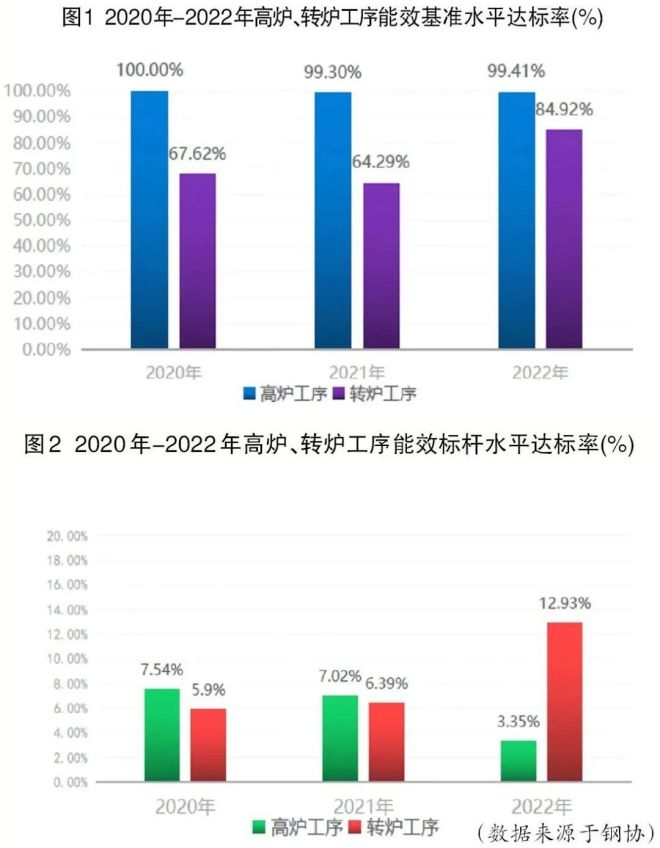
中國鋼鐵工業(yè)協(xié)會(huì )數據顯示,2020年—2022年,高爐工序達到能效基準值的產(chǎn)量占比分別為100%、99.3%、99.41%,達到能效標桿值的比例分別為7.54%、7.02%、3.35%;轉爐工序達到能效基準值的產(chǎn)量占比分別為67.62%、64.29%、84.92%,達到能效標桿值的比例分別為5.9%、6.39%、12.93%??梢?jiàn),鋼鐵行業(yè)高爐工序達到能效基準值的產(chǎn)量占比均在99%以上,遠高于轉爐工序,但整體而言,各主體工序達到能效標桿值的比例,距“2025年能效達到標桿值的產(chǎn)能占比超30%”的政策要求有較大差距。由于高爐經(jīng)濟爐料使用比例上升、節能技術(shù)創(chuàng )新不夠、精細化系統節能意識不足、工序能耗統計口徑存在差異等原因,推進(jìn)主體工序能耗達標工作遇到一定挑戰。
針對國家推進(jìn)的能效標桿、能效約束、極致能效工程,鋼協(xié)發(fā)布《鋼鐵行業(yè)能效標桿三年行動(dòng)方案》,啟動(dòng)開(kāi)展“雙碳最佳實(shí)踐能效標桿示范廠(chǎng)”培育工作,以及“三清單、兩標準、一系統”組合設計,有序推動(dòng)鋼鐵行業(yè)重點(diǎn)工序能效達到標桿,促進(jìn)鋼鐵工業(yè)綠色低碳高質(zhì)量發(fā)展。
“三份清單”包括最佳可行技術(shù)清單、全球范圍內極致能效相關(guān)技術(shù)合作伙伴清單和以國家文件及綠色信貸為主的政策清單。其中,技術(shù)清單是能效達標的關(guān)鍵。面對節能空間日趨縮小的嚴峻形勢,深刻認知鋼鐵流程能源高效轉換的優(yōu)勢,創(chuàng )新能源流網(wǎng)絡(luò )模式、開(kāi)發(fā)高效的能量轉換工藝技術(shù)是破解現階段節能瓶頸的關(guān)鍵。
“兩標準”,一是指《粗鋼生產(chǎn)主要工序單位產(chǎn)品能源消耗限額》(GB21256)和《電弧爐冶煉單位產(chǎn)品能源消耗限額》(GB32050)合并修訂形成的新的強制性國標,已進(jìn)入征求意見(jiàn)階段;二是指《鋼鐵企業(yè)重點(diǎn)工序能效標桿對標指南》(T/CISA 293-2022)團體標準,已于去年發(fā)布。
“一系統”指數據系統,是針對焦爐、高爐、轉爐、電爐重點(diǎn)工序能效對標開(kāi)發(fā)的鋼廠(chǎng)數據填報系統。數據治理是實(shí)現能效對標的基礎,目前基礎仍較為薄弱,國家相關(guān)部委正在推動(dòng)這項工作,鋼鐵行業(yè)也應系統設計、長(cháng)期投入、逐步完善。
我國鋼鐵業(yè)余熱回收利用率低于50%
余熱深度回收及梯級利用水平亟待提升
鋼鐵工業(yè)是流程型制造業(yè),存在復雜的能量消耗、轉換、回收以及輸送過(guò)程,能源流網(wǎng)絡(luò )龐大交錯。
其中,鋼鐵余熱余能資源包括各種煙氣(廢氣)攜帶的顯熱(包括高爐煤氣、轉爐煤氣、焦爐煤氣等可燃氣體),最終軋制成材或材前鐵水、鋼水、坯料具有的顯熱,燒結礦、球團礦具有的顯熱,高爐渣和鋼渣等熔渣顯熱,生產(chǎn)中各種冷卻水及產(chǎn)生的蒸汽攜帶的熱能,高爐爐頂煤氣的余壓,少許帶有壓力的冷卻水,等等。
針對不同品位的余熱資源,鋼企通常采取3種利用方式:第一,對高溫介質(zhì)的顯熱,通常先由蒸發(fā)器進(jìn)行回收,后通過(guò)汽輪機等設備轉換發(fā)電;第二,對中低溫介質(zhì)顯熱,通常進(jìn)行換熱后用于生產(chǎn)過(guò)程,比如供應飽和蒸汽、預熱空氣或煤氣、富余蒸汽用于發(fā)電;第三,對于壓力類(lèi)的余能,通常是利用壓差進(jìn)行膨脹做功。
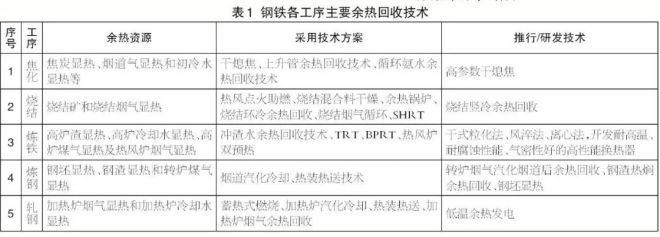
不過(guò),我國鋼鐵企業(yè)在余熱利用方面普遍存在著(zhù)技術(shù)手段少、轉換效率低、回收利用價(jià)值低等問(wèn)題。其中,高溫余熱由于熱量較集中,溫度較高,目前此類(lèi)項目大部分均已有效回收利用。大量的中低溫氣體余熱由于比較分散且熱源波動(dòng),不易集中回收,尚未得到高效回收利用。多數企業(yè)設置蒸汽蓄熱器來(lái)解決余熱資源波動(dòng)問(wèn)題,效果不佳。據研究,我國鋼鐵行業(yè)余熱回收利用率低于50%,還有大量余熱資源直接排放,導致能源浪費。
值得關(guān)注的是,已有部分企業(yè)在余熱利用方面有所突破,如山西新石能源科技有限公司180萬(wàn)噸/年焦化項目配套250噸/小時(shí)干熄焦項目投產(chǎn),實(shí)現噸焦發(fā)電量超過(guò)200千瓦時(shí),比高溫高壓機組提高約15%;建龍西鋼首次應用煙氣隔爆型中低溫余熱回收技術(shù),對180℃以上轉爐煙氣余熱全部回收利用,為行業(yè)開(kāi)展中低溫余熱利用提供了借鑒。下一步,鋼鐵企業(yè)典型工序需持續重點(diǎn)研發(fā)高參數干熄焦、燒結豎冷余熱回收、爐渣干式?;酂峄厥?、轉爐煙氣汽化煙道后余熱回收、爐窯煙氣低溫余熱發(fā)電、中低溫余熱回收等技術(shù)。
聚焦3條路徑
推動(dòng)能源網(wǎng)絡(luò )分布式耦合優(yōu)化
多數鋼鐵企業(yè)存在副產(chǎn)煤氣、余熱蒸汽等二次能源富余的情況。鋼鐵企業(yè)實(shí)施系統節能時(shí),應重點(diǎn)實(shí)施煤氣、蒸汽、余熱系統的能量流網(wǎng)絡(luò )協(xié)同耦合集成優(yōu)化,通過(guò)構建更加合理高效的能量流網(wǎng)絡(luò )實(shí)現系統提升。
分布式能源是相對于集中供能而言的分布式供能方式,利用一切可以利用的資源,輔以集中能源供應系統,實(shí)現直接滿(mǎn)足用戶(hù)多種需求的能源梯級利用,達到更高的能源綜合利用效率。鋼鐵能源網(wǎng)絡(luò )分布式耦合優(yōu)化的重點(diǎn)在于,實(shí)現鋼鐵生產(chǎn)工藝過(guò)程與“源-網(wǎng)-荷-儲”分布式能源系統的充分耦合,實(shí)現煤氣、蒸汽等能源網(wǎng)絡(luò )的互聯(lián)互儲,具體實(shí)施路徑包括煤氣平衡優(yōu)化、分布式蒸汽自平衡及優(yōu)化、煤氣—蒸汽—電力協(xié)同優(yōu)化調度等。
煤氣平衡優(yōu)化。煤氣系統優(yōu)化應遵循“極限回收、高效使用、能級匹配、高效轉化和零放散”的原則,根據煤氣資源的數量、品質(zhì)和用戶(hù)需求不同,高效分配使用煤氣,完善煤氣緩沖系統,優(yōu)化煤氣管網(wǎng),實(shí)現煤氣閉環(huán)管理和零放散。同時(shí),可應用蓄熱式燃燒等高效燃燒技術(shù)措施適應工藝用戶(hù)的熱工需求,以解決部分企業(yè)等效替代的煤氣結構平衡問(wèn)題。
鋼企應科學(xué)制訂煤氣平衡方案,不能只關(guān)注靜態(tài)平衡要素,還要從生產(chǎn)角度出發(fā)推動(dòng)實(shí)現動(dòng)態(tài)平衡。包括結合實(shí)際情況做好高爐休風(fēng)、軋鋼產(chǎn)線(xiàn)調整等多個(gè)因素的分析,掌握各種關(guān)鍵性因素。減緩熱風(fēng)爐等高爐煤氣“大用戶(hù)”的峰谷起伏,對于提升整個(gè)高爐煤氣系統的穩定性至關(guān)重要。為此,鋼企應通過(guò)對熱風(fēng)爐的燒爐時(shí)間進(jìn)行整體安排,避免發(fā)生因熱風(fēng)爐大燒、小燒時(shí)間重疊引起的高爐煤氣峰谷用量波動(dòng)。
鋼企還應構建具備較高能力的煤氣緩沖系統,配備相應規模的煤氣柜;通過(guò)獎勵減少放散量的單位等經(jīng)濟手段,引導各單位向有利于煤氣平衡的方向發(fā)展,激勵各單位積極探究節能降耗措施,提高煤氣利用效率。
分布式蒸汽自平衡及優(yōu)化。提高余熱、余壓的回收利用水平,采用技術(shù)先進(jìn)、經(jīng)濟合理的節能工藝、技術(shù)、設備與措施,按照“高質(zhì)高用、梯級利用、能級匹配、耦合協(xié)同”的科學(xué)用能原則,實(shí)現能源的就地轉換利用。
鋼企可以考慮不同能源介質(zhì)的經(jīng)濟輸送半徑,建立多個(gè)區域性能源利用體系。例如,焦化區域通過(guò)實(shí)施上升管余熱回收、負壓蒸氨和負壓脫苯技術(shù)改造、循環(huán)氨水余熱回收等節能技術(shù)項目,實(shí)現焦化蒸汽自供應,減少干熄焦抽汽,也能避免蒸汽管網(wǎng)長(cháng)距離輸送造成的能源損失。再如,在高爐、焦化、燒結區域分別回收相應余熱,作為吸收式制冷系統驅動(dòng)的熱源,使整個(gè)系統按能源品位進(jìn)行分級利用和循環(huán)利用。
鋼企還可改革以蒸汽為載體的能源運行方式,建立以熱導油、高壓熱水為載體的能量流網(wǎng)絡(luò )。包括減少設置甚至取消蒸汽管網(wǎng),余熱蒸汽高參數回收、就地發(fā)電上網(wǎng),構建科學(xué)、合理、高效的能源網(wǎng)絡(luò );針對RH(真空循環(huán)脫氣)等間斷用戶(hù)的生產(chǎn)情況,煉鋼工序應開(kāi)發(fā)高效機械真空系統,替代蒸汽噴射。如湛江鋼鐵燒結系統就采用“機上爐”技術(shù),直接在燒結環(huán)冷機上布置余熱鍋爐,避免煙氣長(cháng)距離導引的熱損失,并根據余熱資源配備補汽式發(fā)電機組,利用煤氣產(chǎn)生低壓蒸汽,確保燒結余熱發(fā)電機組的穩定高負荷運行。
煤氣—蒸汽—電力協(xié)同優(yōu)化調度。煤氣、蒸汽、電力是鋼鐵企業(yè)能源系統中重要的二次能源,并且相互之間存在轉換。鋼鐵企業(yè)可以通過(guò)煤氣、蒸汽、電力3種能源的協(xié)同轉換和優(yōu)化使用,推進(jìn)節能減排和能源成本降低。由于歷史原因,鋼鐵流程中的煤氣、蒸汽、電力能源均處于無(wú)序狀態(tài),特別是操作換向工藝波動(dòng)會(huì )造成放散損失。要實(shí)現二次能源高效閉環(huán)有序運行,必須建立以?xún)δ転楹诵牡男履茉淳彌_及高效轉化能控中心,同時(shí)在確保能源穩定供應和安全生產(chǎn)的前提下,優(yōu)化富余煤氣分配以及蒸汽、電力需求的生產(chǎn)調度,使調度周期內系統能源成本降到最低。
抓牢煤氣發(fā)電機組改造“關(guān)鍵抓手”
力促煤氣發(fā)電(自發(fā)電)能效提升
提升自發(fā)電水平是提高流程能源轉換效率、降低能源成本最直接、提升效益最明顯的抓手。余熱余能自發(fā)電影響噸鋼能源成本約100元以上,對鋼鐵企業(yè)效益及競爭力高低影響較大。鋼鐵余熱余能發(fā)電技術(shù)主要包括煤氣發(fā)電、干熄焦發(fā)電、高爐干式余壓發(fā)電、燒結余熱發(fā)電等。其中,煤氣發(fā)電占比最大,抓好這項工作,將對企業(yè)的自發(fā)電提升和能效提升起到?jīng)Q定性的影響。
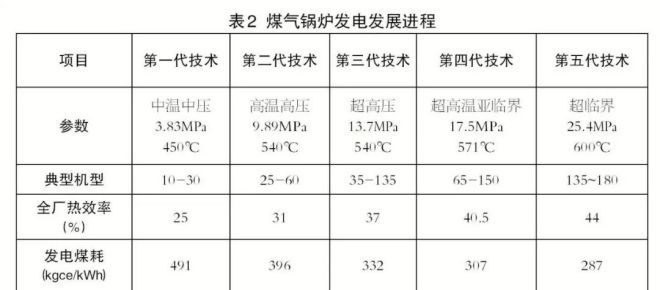
根據發(fā)電原理不同,鋼鐵行業(yè)煤氣發(fā)電機組分為燃氣—蒸汽聯(lián)合循環(huán)發(fā)電(CCPP)機組和鍋爐發(fā)電機組。煤氣鍋爐發(fā)電技術(shù)近年來(lái)快速發(fā)展,由原來(lái)的中溫中壓、高溫高壓發(fā)展到目前主流的超高壓、亞臨界、超臨界參數,高爐煤氣單耗由5立方米/千瓦時(shí)降至2.4立方米/千瓦時(shí),先進(jìn)機組的熱效率達到44%。很多鋼鐵企業(yè)通過(guò)主動(dòng)淘汰中、低參數機組并結合高爐汽動(dòng)鼓風(fēng)改造,集中煤氣資源建設超高壓、亞臨界、超臨界機組,獲得了較高效益。高參數機組在小型化方面的技術(shù)突破,為在中小型鋼鐵企業(yè)中推廣創(chuàng )造了條件,35兆瓦~65兆瓦等級超高壓及65兆瓦~150兆瓦等級亞臨界煤氣發(fā)電均已有上百臺(套)成熟工程案例,盛隆冶金、津西鋼鐵等企業(yè)150兆瓦等級超臨界機組建成投運。其中,3×145兆瓦超臨界煤氣發(fā)電機組安全高效穩定運行一年有余,發(fā)電效率達到43.5%,2022年3臺機組累計發(fā)電18.8億千瓦時(shí)。山西建邦集團通才公司通過(guò)系統節能以及煤氣發(fā)電機組升級改造,實(shí)現在沒(méi)有焦化工序的情況下,自發(fā)電率超過(guò)80%。
目前在鋼鐵行業(yè),中溫中壓機組的應用很少,基本上已經(jīng)停下來(lái)作為備用機組;還有一定數量的高溫高壓機組,少數企業(yè)有高溫高壓汽動(dòng)鼓風(fēng),將在“十四五”期間全部改造完成。預計到“十四五”末,鋼鐵行業(yè)35兆瓦等級以下會(huì )保留少量的高溫高壓機組,35兆瓦~5兆瓦等級的煤氣發(fā)電全部為超高壓機組、65兆瓦~100兆瓦等級煤氣發(fā)電為亞臨界機組、100兆瓦~180兆瓦等級煤氣發(fā)電為超臨界(亞臨界)機組,且新建的機型多數為超臨界機組。據筆者了解,相關(guān)公司正在對100兆瓦燃氣—蒸汽聯(lián)合循環(huán)發(fā)電(CCPP)進(jìn)行攻關(guān),設計發(fā)電效率將超過(guò)50%,屆時(shí)投運后該機型的競爭力將明顯優(yōu)于現有機型,也將為鋼鐵企業(yè)煤氣發(fā)電多一條選擇路徑。
煤氣發(fā)電能效提升、自發(fā)電提升工作同樣是一項系統工程,需促進(jìn)高能效轉化工藝、裝備、管理技術(shù)創(chuàng )新開(kāi)發(fā),特別要在分布式能源耦合集成優(yōu)化、科學(xué)制定煤氣平衡、兼顧高效與安全可靠性、開(kāi)展技術(shù)經(jīng)濟比選以保效益最大化、向高參數機組發(fā)展、高標準開(kāi)展項目設計施工等方面采取措施,提高自發(fā)電水平。
打破能源轉化的行業(yè)壁壘
實(shí)現跨行業(yè)協(xié)同與碳氫元素原料耦合利用
現有鋼鐵生產(chǎn)流程中的焦化副產(chǎn)品化產(chǎn)利用、副產(chǎn)煤氣及余熱發(fā)電、高溫熔渣制備水泥及其他建材等技術(shù)已實(shí)現規?;a(chǎn),具有跨冶金、化工、電力、建材等行業(yè)聯(lián)產(chǎn)的特征??缧袠I(yè)協(xié)同與碳氫元素原料耦合利用將成為鋼鐵工業(yè)實(shí)現更大范圍系統節能的重要途徑和運營(yíng)模式。
筆者認為,基于能源綜合梯級利用原理,以提高系統能效為目標,在工業(yè)園區等跨行業(yè)聯(lián)產(chǎn)系統總體規劃的基礎上,通過(guò)能源綜合梯級利用和橫向多行業(yè)互補,打破能源轉化在行業(yè)間的壁壘,實(shí)現行業(yè)內和跨行業(yè)不同能源形式的耦合利用,可進(jìn)一步提高全社會(huì )整體能源利用效率,是當前及未來(lái)能源可持續發(fā)展的重要技術(shù)路徑。主要包括以下幾個(gè)方向:煤氣充當周邊水泥窯等的燃料、副產(chǎn)煤氣用于化產(chǎn)、余熱蒸汽用于海水淡化、余熱供暖(供冷)等,使鋼鐵企業(yè)成為社區、城市的清潔能源供應中心。
煤氣、蒸汽用于周邊企業(yè)燃料及熱源。從能效及經(jīng)濟性角度考慮,對于附近有其他產(chǎn)業(yè)的鋼鐵企業(yè)而言,把副產(chǎn)煤氣、蒸汽外售的經(jīng)濟性要優(yōu)于發(fā)電利用。鞍鋼鲅魚(yú)圈通過(guò)外銷(xiāo)煤氣給華能、外銷(xiāo)蒸汽給嘉里糧油,每年創(chuàng )效近8000萬(wàn)元;南京鋼鐵通過(guò)華潤壓縮空氣等能源保供模式創(chuàng )新,實(shí)現區域能源供應有效協(xié)同。
副產(chǎn)煤氣用于化產(chǎn),實(shí)現降碳、固碳和高價(jià)值利用。副產(chǎn)煤氣中含有CO、H2和CH4等成分,可以作為化工合成的基本原料氣。焦爐煤氣制備的化工產(chǎn)品主要有天然氣、甲醇、乙醇、乙二醇等。此外,焦爐煤氣還可以用于合成氨進(jìn)而生產(chǎn)尿素化肥等,從焦爐煤氣中分離提取的氫也是重要的氫能來(lái)源。轉爐煤氣提純的CO可與焦爐煤氣分離的H2結合,合成乙醇、乙二醇或者生產(chǎn)草酸、甲酸等化工產(chǎn)品,也可以采取發(fā)酵蒸餾的方式,通過(guò)加入氨制成燃料乙醇,同時(shí)產(chǎn)生副產(chǎn)沼氣和蛋白粉飼料。目前,已有很多鋼企在這方面開(kāi)展了應用,如山鋼日照、河北安豐等企業(yè)建有焦爐煤氣制天然氣裝置,滄州中鐵、達州鋼鐵、黑龍江建龍等建設了焦爐煤氣聯(lián)合高爐煤氣制甲醇裝置,晉南鋼鐵建設了焦爐煤氣聯(lián)合轉爐煤氣制乙二醇裝置,石橫特鋼建設了轉爐煤氣制甲酸裝置。
余熱蒸汽用于海水淡化。低溫多效蒸餾(LT-MED)海水淡化所需溫度低,采用抽引凝結換熱、氣液兩相防腐換熱、熱水高效閃蒸及蒸汽抽射增壓等技術(shù),可回收鋼鐵低品質(zhì)余熱作為L(cháng)T-MED海水淡化裝置的熱源。這一技術(shù)已在首鋼京唐應用,該方法實(shí)現了能源的梯級利用,以及蒸汽、煤氣、工業(yè)廢水及濃海水的零排放。
余熱供暖(供冷)、建設城市余能利用中心。鋼企充分開(kāi)發(fā)利用低品位余熱、沖渣水余熱、煙氣余熱等,可為周邊社區、城市供暖供熱,減少地區燃煤設施及相應的碳排放。目前,鋼鐵企業(yè)的高品質(zhì)余熱已基本得到利用,下一步需要深度挖掘余熱資源與節能技術(shù)改造,利用生產(chǎn)余熱供應周邊冬季供熱及生活熱水,推進(jìn)產(chǎn)城融合,實(shí)現共融發(fā)展。據筆者了解,截至2022年底,撫順新鋼鐵社會(huì )供暖面積達887萬(wàn)平方米,噸鋼供暖面積達到世界領(lǐng)先水平(2.2平方米)。
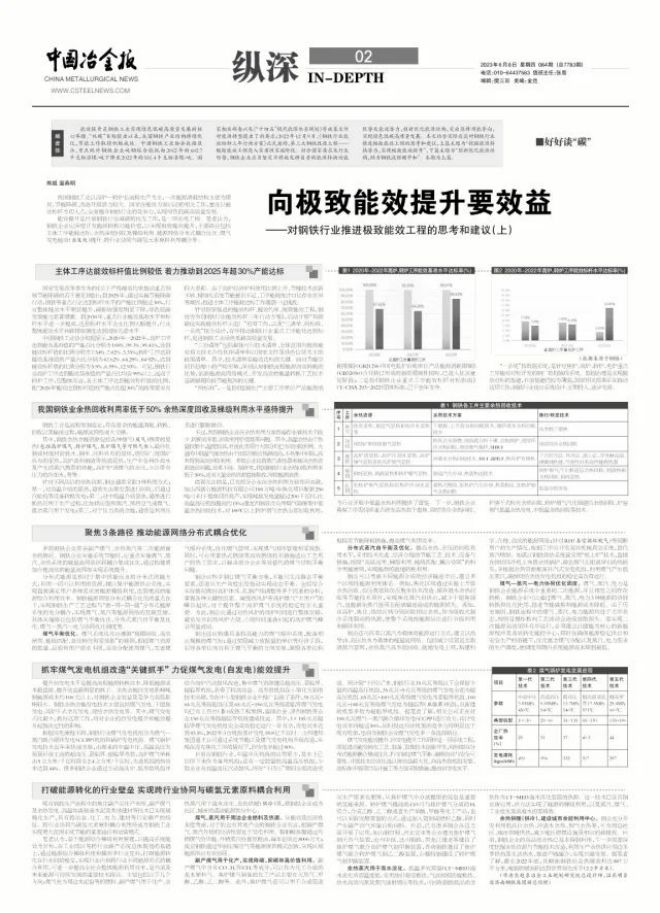
(熊超 溫燕明(作者熊超系冶金工業(yè)規劃研究院總設計師,溫燕明系原濟南鋼鐵集團副總經(jīng)理))