摘 要:高爐煤氣由于熱值和燃燒效率低而被大量放散,采用Cu系吸附劑變壓吸附工藝提純高爐煤氣中的CO,提高其熱值和燃燒效率,用于下游生產(chǎn),對于節能降耗和保護環(huán)境有著(zhù)非常重要的意義。
前 言
我國是鋼鐵生產(chǎn)大國,近年來(lái)生鐵產(chǎn)量呈逐年上升趨勢。目前, 鋼鐵工業(yè)總能耗已占全國工業(yè)總能耗的15%左右。在鋼鐵聯(lián)合企業(yè),高爐煉鐵又是能耗最高的環(huán)節。鋼鐵工業(yè)的節能主要包括減少浪費和增加回收兩個(gè)方面,其中大力回收生產(chǎn)過(guò)程中產(chǎn)生的二次能源(例如副產(chǎn)煤氣等)是一個(gè)非常重要的途徑。鋼鐵生產(chǎn)過(guò)程中的副產(chǎn)煤氣資源包括高爐煤氣、焦爐煤氣和轉爐煤氣。其中高爐煤氣排放量約占64%, 焦爐煤氣約占29 % , 轉爐煤氣約占7%, 因此高爐煤氣的有效利用是鋼廠(chǎng)節能降耗的重中之重。
高爐煤氣是高爐煉鐵過(guò)程中的副產(chǎn)煤氣,是一種無(wú)色、無(wú)味、有毒的低熱值氣體燃料。其主要成分為CO、CO2、N2 、H2O及少量H2,各成分的含量與高爐所用燃料、生鐵品種和冶煉工藝密切相關(guān),其常見(jiàn)的組成如表1所示。
其中最具有二次利用價(jià)值的CO含量?jì)H為25%~30%,而惰性組分CO2和N2約占70%,使得高爐煤氣的熱值很低,一般僅為(730~800)×4.18 kJ/Nm3左右,而燃料熱值只有達到2200×4.18kJ/Nm3左右,才能滿(mǎn)足工業(yè)爐理論燃燒溫度的要求。
目前,高爐煤氣的利用并不充分,大部分冶金工廠(chǎng)高熱值煤氣緊缺,而高爐煤氣富余,存在不同程度的高爐煤氣放散現象,達不到煤氣的有效利用。很多鋼鐵聯(lián)合企業(yè)一方面在放散高爐煤氣,一方面又要購入重油、天然氣或者燒自產(chǎn)焦油等作為能源補充。高爐自身熱風(fēng)爐會(huì )用掉40 %~50 % 的高爐煤氣, 其余大部分如果放散到大氣中,將會(huì )造成環(huán)境的污染和能源的浪費。國家有關(guān)部門(mén)頒發(fā)的《中國節能技術(shù)政策大綱》中要求, 冶金重點(diǎn)企業(yè)高爐煤氣排放損失率應為4 %以下。
目前,在冶金聯(lián)合企業(yè)生產(chǎn)中,高爐煤氣可以用于熱風(fēng)爐、煉焦、加熱爐和發(fā)電等,具體利用途徑如下:一是高爐煤氣用于軋鋼加熱爐,采用蓄熱式燃燒技術(shù)。應用高溫空氣燃燒技術(shù), 將高爐煤氣與助燃空氣雙預熱到1000 ℃ 以上, 使單一高爐煤氣的理論燃燒溫度達到2200 ℃ 以上,熱效率高于常規加熱爐約30%。蓄熱式燃燒爐難以控制供氣、爐壓穩定和燃燒穩定,改造時(shí)間長(cháng)、維護成本高。二是高爐煤氣與高熱值氣體燃料混合,配成滿(mǎn)足加熱爐使用要求的次高熱值燃料。高爐煤氣可與焦爐煤氣、天然氣、液化石油氣等混合, 作為均熱爐、加熱爐、熱處理爐等爐子的燃料, 并可用于燒結機點(diǎn)火、加熱熱軋的鋼錠、預熱鋼水包等。三是高爐煤氣用于燒鍋爐,滿(mǎn)足工廠(chǎng)用蒸汽的同時(shí)再發(fā)電。高爐煤氣蒸汽聯(lián)合循環(huán)發(fā)電(簡(jiǎn)稱(chēng)CCPP)效率高、成本低, 但建設投資巨大。四是單獨預熱高爐煤氣,提高軋鋼的入爐溫度。
北京北大先鋒科技有限公司于2012年為華菱衡鋼設計建成PSA高爐煤氣提濃CO裝置,采用變壓吸附技術(shù),利用Cu系吸附劑從高爐煤氣中分離提純CO。變壓吸附法具有投資少、操作彈性大、自動(dòng)化程度高、操作簡(jiǎn)單等優(yōu)點(diǎn),而Cu系吸附劑相比常規變壓吸附使用的5A分子篩,對于CO和N2有更大的分離系數,尤其適合從氮氣含量高的高爐煤氣中將CO提純出來(lái)。
采用Cu系吸附劑變壓吸附法
提純高爐煤氣中CO工藝
本文以投產(chǎn)的湖南衡鋼百達先鋒能源科技有限公司高爐煤氣變壓吸附提純CO裝置為例,介紹了采用北大先鋒變壓吸附技術(shù)分離CO的應用情況。裝置設計收率92%,CO產(chǎn)品氣濃度根據用戶(hù)需要在60%~70%范圍內可調,產(chǎn)品氣作為燃料用于鋼管加工。設計流程圖、原料氣組成及產(chǎn)品氣要求如圖1、表2、表3所示。
工藝流程
由于高爐煤氣中含有微量的COS、O2等雜質(zhì),而且含量不穩定,本工藝設計了預處理工序。該工序采用脫硫和除氧工藝,脫硫塔和除氧塔中裝填北大先鋒專(zhuān)有的脫硫劑和除氧劑,使高爐煤氣中的總硫在進(jìn)入變壓吸附工序之前被脫除至1ppm以下, O2被脫除至5ppm以下。
脫硫工藝采用干法脫硫,主要包括常溫水解、粗脫硫、精脫硫三個(gè)步驟。在水解步驟中,大部分的COS被水解成H2S,水解率大于95%;水解后的氣體經(jīng)過(guò)粗脫硫后,絕大部分H2S被脫硫劑吸附;剩余的COS和H2S經(jīng)過(guò)精脫硫吸收后,總硫脫除至1ppm以下。除氧工藝采用北大先鋒自主研制開(kāi)發(fā)的PU-5除氧劑,在CO氛圍下,催化微量O2和CO進(jìn)行反應,將O2脫除至5ppm以下。
PSA-CO工序采用變壓吸附分離工藝,經(jīng)過(guò)預處理后的潔凈氣體在PSA-CO工序中經(jīng)過(guò)吸附、均壓降壓、順?lè )?、抽真空、均壓升壓、終充壓循環(huán)過(guò)程分離提純CO。CO作為產(chǎn)品氣常壓析出,經(jīng)過(guò)壓縮機壓縮到用戶(hù)要求壓力,外送至用戶(hù)使用處。PSA-CO工序采用了北大先鋒開(kāi)發(fā)的分離CO高效吸附劑,在未使用置換步驟的前提下,不但滿(mǎn)足CO產(chǎn)品的高純度要求,同時(shí)節省了一次性投資和運行費用,流程相對簡(jiǎn)化,操作變得簡(jiǎn)單易控。
裝置實(shí)際運行結果分析
該高爐煤氣提純CO裝置從2013年6月8日一次性開(kāi)車(chē)成功后一直運行穩定,而且在高爐生產(chǎn)波動(dòng)較大時(shí)也能滿(mǎn)足各種工況下的使用要求。實(shí)際運行72小時(shí)測得平均產(chǎn)品氣規格(氣相色譜外標法)如下。
實(shí)際運行中,高爐煤氣中的COS濃度經(jīng)常發(fā)生變化,在50ppm~120ppm之間波動(dòng),預處理工序通過(guò)溫度的適當調整能完全脫除COS。
高爐煤氣中CO含量的設計值為24%,但實(shí)際運行過(guò)程中只有18%~22%,在這種濃度范圍內,CO產(chǎn)品氣中的CO含量還能達到設計要求。當原料氣中CO濃度>20%時(shí),產(chǎn)品氣中CO濃度>72%。
平均高爐煤氣消耗量為60000Nm3/h,CO產(chǎn)品氣量為18000Nm3/h,收率在93%左右,產(chǎn)品純度可根據需要在60%~70%范圍內調節,完全滿(mǎn)足衡鋼下游工序的熱值需求,節能效果顯著(zhù)。按照產(chǎn)品氣與天然氣的熱值計算,CO產(chǎn)品氣每小時(shí)可代替天然氣4537m3,年代替量達到3974×104m3,相當于衡鋼原來(lái)約1/3的天然氣用量,很大程度上緩解了衡鋼用氣緊張的局面。
總 結
高爐煤氣中含有豐富的CO氣體,具有很高的利用價(jià)值。利用北大先鋒的Cu系吸附劑變壓吸附工藝分離提純高爐煤氣中CO氣體,將高爐氣中CO組分含量從22%(熱值731kcal/Nm3)提純到70%(熱值2200kcal/Nm3),作為燃料氣用于鋼管加工,在節能降耗方面有著(zhù)重要意義。另外,利用該項技術(shù)還能將高爐煤氣中的CO濃度提至98.5%以上,從而用于化工生產(chǎn),合成乙二醇、碳酸二甲酯、醋酸、甲醇、TDI、DMF等,這不但實(shí)現了鋼鐵和化工兩個(gè)行業(yè)的資源整合,具有良好的經(jīng)濟效益,還有助于降低鋼鐵和化工企業(yè)整體的一次能源使用量,從而降低二氧化碳排放量,促進(jìn)產(chǎn)業(yè)耦合,推動(dòng)行業(yè)實(shí)現綠色、低碳、可持續發(fā)展。
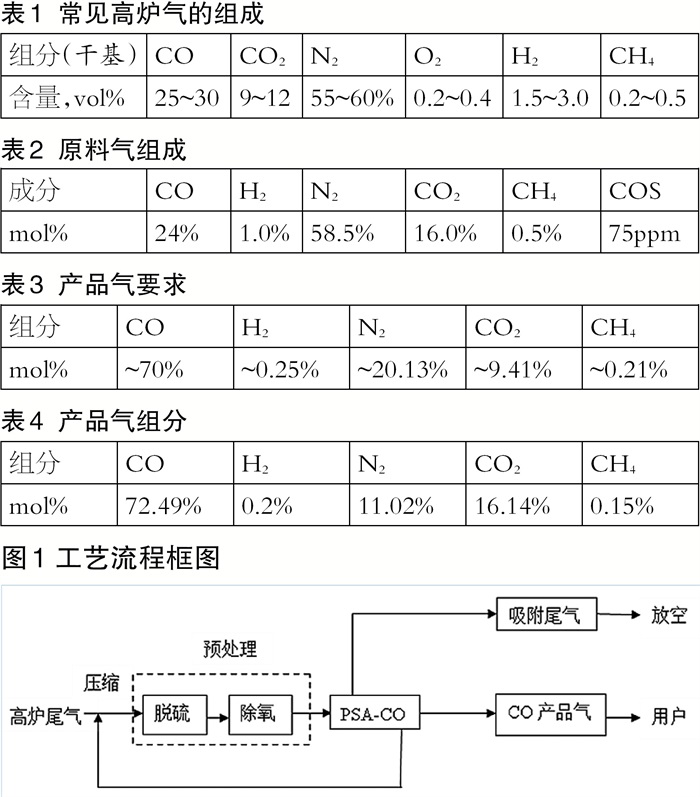
作者:顧光臨