河鋼全球首例120萬(wàn)噸氫冶金示范工程(以下簡(jiǎn)稱(chēng)氫冶金示范工程),是氫作為大工業(yè)生產(chǎn)能源應用的第一例。連日來(lái),氫冶金示范工程實(shí)現安全順利連續生產(chǎn)綠色DRI產(chǎn)品。目前,DRI產(chǎn)品金屬化率達到94%,關(guān)鍵指標完全達到合格產(chǎn)品標準,可作為高端材料制造高品質(zhì)潔凈原料,是替代電爐廢鋼特別是高品質(zhì)廢鋼的重要原料。這標志著(zhù)項目一期工程取得圓滿(mǎn)成功,成為中國鋼鐵史乃至世界鋼鐵史上由傳統“碳冶金”向新型“氫冶金”轉變的一個(gè)重要的里程碑。
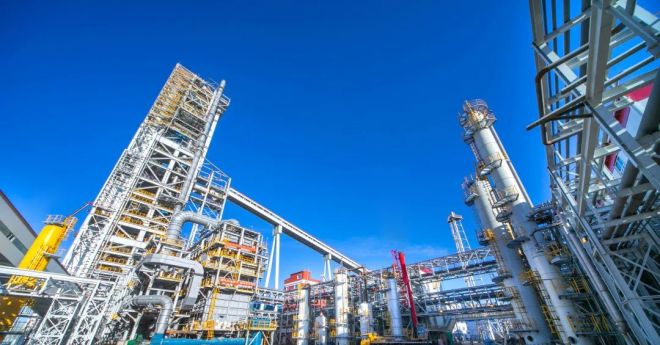
黨的二十大報告指出,“立足我國能源資源稟賦,堅持先立后破,有計劃分步驟實(shí)施碳達峰行動(dòng)?!?在全球能源向清潔化、低碳化、智能化發(fā)展的趨勢下,鋼鐵行業(yè)無(wú)論是能源結構創(chuàng )新還是工藝結構創(chuàng )新,氫能應用都是實(shí)現低碳、甚至“零碳”排放的最佳途徑。
作為鋼鐵行業(yè)綠色轉型的先行者,河鋼堅定與國家“雙碳”戰略同向同行,深耕氫能與鋼鐵的融合創(chuàng )新、協(xié)同發(fā)展,超前跟蹤世界氫冶金技術(shù)的研究與發(fā)展,與意大利特諾恩等知名企業(yè)合作,建設了氫冶金示范工程。
該工程對突破氫冶金核心關(guān)鍵技術(shù)和推動(dòng)我國鋼鐵行業(yè)轉型升級具有重大引領(lǐng)作用,為我國鋼鐵行業(yè)“擺脫”對煤炭等傳統化石能源的深度依賴(lài)提供了全新路徑、創(chuàng )造了全新場(chǎng)景。
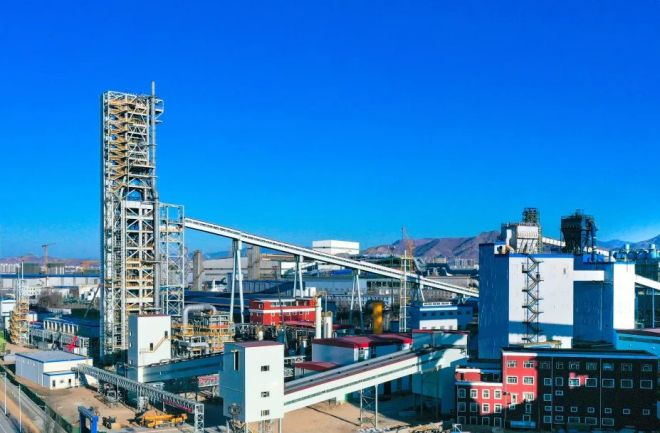
河鋼氫冶金示范工程打破國際上采用天然氣制備還原工藝氣體的常規手段,首創(chuàng )“焦爐煤氣零重整豎爐直接還原”工藝技術(shù),充分發(fā)揮豐富的焦爐煤氣資源優(yōu)勢,創(chuàng )新采用焦爐煤氣作為氣基。作為可以直接利用的氫能源,焦爐煤氣含有55%—65%的氫氣成分,可在氫基豎爐內催化裂解為CO和H?,實(shí)現“自重整”。自重整后,工藝氣體中的氫碳比可達到8:1以上,是目前工業(yè)化生產(chǎn)中含氫比例最高的氣基豎爐直接還原工藝,最接近未來(lái)100%氫還原的工藝狀態(tài)。同時(shí),河鋼氫冶金示范工程豎爐反應器針對高比例氫含量進(jìn)行了優(yōu)化設計,預留了綠氫切換功能,不需大規模改造即可直接開(kāi)展切換為更高比例富氫還原氣、純氫作還原氣的工業(yè)試驗,為未來(lái)實(shí)現100%綠氫豎爐直接還原提供基礎。
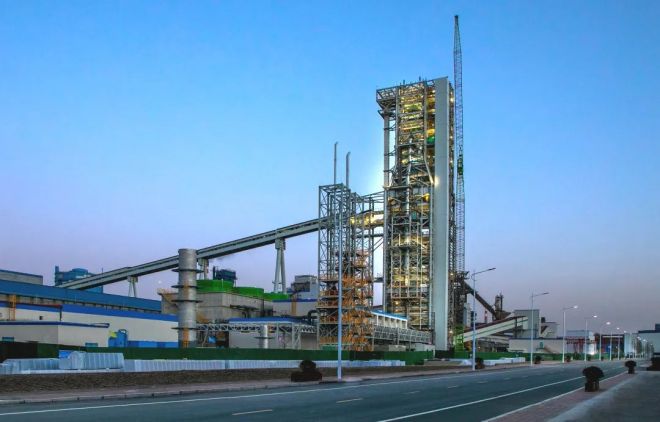
此外,河鋼還研發(fā)出具有國際領(lǐng)先水平的“CO?捕集+CO?精制”技術(shù),形成了包含《全氧富氫低碳還原熔化煉鐵系統及煉鐵方法》《控制氮氣富集的氣基直接還原煉鐵方法及系統》等30項氫冶金專(zhuān)利技術(shù)的綠色短流程工藝,打造出可推廣、可復制的“零碳”制氫與氫能產(chǎn)業(yè)發(fā)展協(xié)同互補的創(chuàng )新發(fā)展模式。
據測算,與同等生產(chǎn)規模的傳統“高爐+轉爐”長(cháng)流程工藝相比,河鋼氫冶金示范工程一期每年可減少CO?排放80萬(wàn)噸,減排比例達到70%以上,同時(shí)SO?、NOx、煙粉塵排放分別減少30%、70%和80%以上,且生產(chǎn)每噸直接還原鐵可捕集CO?約125千克。
作為氫冶金技術(shù)的先行者、踐行者和探索者,河鋼在不斷探索并引領(lǐng)氫冶金技術(shù)的同時(shí),還積極與強者為伍,構建綠色低碳鋼鐵供應鏈。
去年8月,河鋼與寶馬簽署了《打造綠色低碳鋼鐵供應鏈合作備忘錄》,從2023年中期開(kāi)始,寶馬沈陽(yáng)生產(chǎn)基地量產(chǎn)車(chē)型將逐步使用河鋼的低碳汽車(chē)用鋼;從2026年起,寶馬沈陽(yáng)生產(chǎn)基地將開(kāi)始在整車(chē)量產(chǎn)過(guò)程中使用河鋼生產(chǎn)的綠色汽車(chē)用鋼(簡(jiǎn)稱(chēng)“綠鋼”)。這些“綠鋼”基于綠電和電爐等工藝,其生產(chǎn)過(guò)程將逐步實(shí)現減少CO?排放量95%。
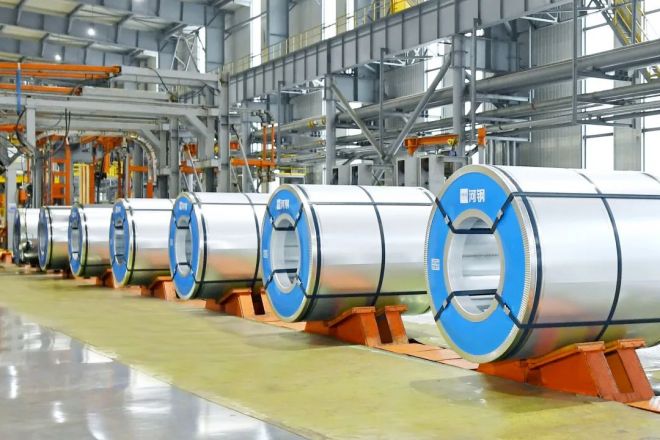
厚植氫能,就是厚植未來(lái)。以氫冶金示范工程一期圓滿(mǎn)成功為新起點(diǎn),河鋼將把氫能開(kāi)發(fā)利用作為重點(diǎn)發(fā)展方向,加快推進(jìn)低碳冶金技術(shù)的革命性創(chuàng )新與突破,積極引領(lǐng)鋼鐵行業(yè)氫能綜合利用與發(fā)展,為全球鋼鐵行業(yè)綠色低碳發(fā)展提供更多更好的“河鋼方案”。